In the context of the fast-moving consumer goods and pharmaceutical industries posing the triple challenges of "high flexibility, high precision, and high compliance" to packaging equipment, Shanghai Acepack Intelligent Packaging Technology Co., Ltd. (Acepack) has become the core promoter of industry upgrading with its filling and capping machine technology system. By deeply integrating European design concepts with localized innovation, the company's equipment has achieved full scene coverage from daily chemical products to biopharmaceuticals, and has led the formulation of a number of industry technical standards.
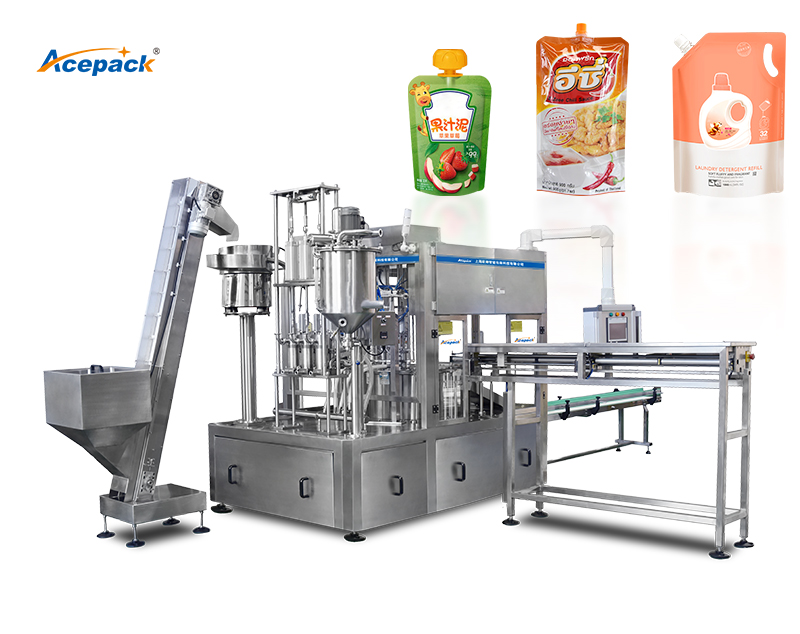
1. Flexible production: full servo drive architecture reconstructs packaging logic
Shanghai Acepack's filling and capping machine is based on a full servo drive system, and realizes independent adjustment of the three modules of filling, capping, and conveying through PLC+industrial PC dual-core control. Taking the AS-8000 equipment as an example, its filling module uses dual servo motors to synchronously control the metering pump and needle movement, and the filling accuracy can reach ±0.3ml (based on 200ml of liquid), which is 60% higher than traditional equipment. In the capping process, the equipment is equipped with a seven-station adaptive capping head, which monitors the capping torque in real time through a torque sensor (accuracy ±0.05N·m), and dynamically adjusts the speed and pressure in combination with the AI algorithm, so that the tightening pass rate of anti-theft caps, threaded caps, and child safety caps exceeds 99.8%.
In response to the needs of special-shaped packaging, Oushuo has developed a three-in-one system of roll film bag making-filling-capping. Take self-supporting bag packaging as an example:
Roll film bag making module: using ultrasonic sealing technology, the bag body is heat-sealed within 0.1 seconds, and the sealing strength reaches 25N/15mm, which is 67% higher than the industry standard;
Filling module: using negative pressure suction technology to avoid liquid hanging on the wall, the filling speed can reach 3000 bags/hour (calculated based on 100ml specifications);
Capping module: integrated visual positioning system, scanning the nozzle position at a speed of 0.05 seconds/frame to ensure that the deviation between the capping head and the nozzle center is ≤0.1mm.
A case study of a daily chemical company shows that Oushuo's equipment can achieve rapid switching of bottle mouth diameters from 12 to 100 mm and filling ranges from 100 to 1000 ml through modular design. The changeover time is compressed to 25 minutes, which is 55% more efficient than traditional models.
2. Pharmaceutical-grade compliance: dual guarantee of sterile barrier and data traceability
Facing the strict requirements of the pharmaceutical industry for "zero defect rate" and "full process traceability" of packaging equipment, Oushuo launched a GMP-grade filling and capping machine, the core breakthrough of which is:
Sterile barrier system: adopts the combination design of laminar flow hood + HEPA filter to achieve ISO 5 (Grade A) cleanliness in the filling area, and completes the surface disinfection of the equipment within 15 minutes through the ozone sterilization module (killing rate ≥ 99.99%);
Torque intelligent closed-loop control: The torque data of each bottle capping is uploaded to the PLC in real time to generate a traceable torque curve map to meet the FDA 21 CFR Part 11 electronic record specification;
Negative pressure leakage detection: -80kPa vacuum pressure is applied to the bottle after capping, and it is automatically rejected when the leakage rate exceeds 0.01kPa/s within 30 seconds to ensure the integrity of the seal.
In the cell preservation solution packaging scenario, Oushuo equipment uses vacuum negative pressure filling technology, dynamically adjusts the filling pressure through a pressure sensor (accuracy ±0.1kPa) to avoid bubble generation, and the filling qualification rate reaches 99.95%. Its equipment has passed the ISO 13485 medical device quality management system certification and has achieved a coverage rate of more than 85% in the top 10 domestic biopharmaceutical companies.
3. Full life cycle management: from energy consumption optimization to predictive maintenance
Oushuo filling and capping machines achieve full life cycle cost reduction through hardware upgrades and software empowerment:
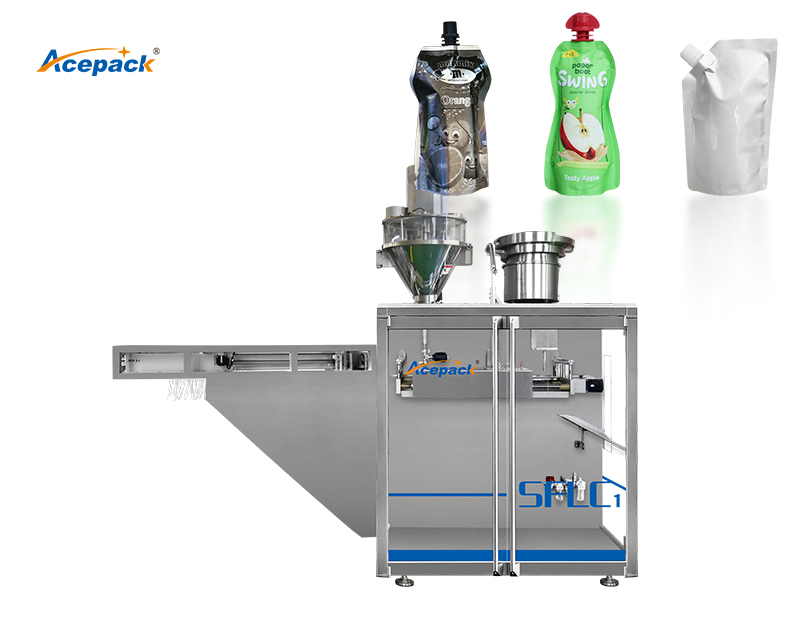
Permanent magnet synchronous motor + energy feedback technology: enables a single machine to save 23,000 kWh of electricity per year, reducing energy consumption by 35% compared to traditional models;
Digital twin predictive maintenance: Real-time monitoring of the health status of the spindle and cam mechanism through vibration sensors (accuracy ±0.01g) and temperature sensors (accuracy ±0.5℃), combined with LSTM neural networks to predict the remaining service life (RUL), reducing unplanned downtime by 70%;
Ceramic-carbide composite coating capping head: Increase the life of the capping head from 3 million times to 10 million times, and reduce the annual maintenance cost of a single capping module by 50%.
In a dairy company's production line, Oushuo equipment integrates the MES interface to realize real-time upload of data such as filling volume, capping torque, and operating time, supporting enterprises to optimize production scheduling through OEE (overall equipment efficiency) analysis, and increase overall capacity utilization by 22%.
Conclusion: Technology reconstructs the packaging value chain
Shanghai Oushuo filling and capping machine has redefined the value boundary of packaging equipment through flexible architecture, pharmaceutical-grade compliance design and full life cycle management. Its technical system not only solves traditional pain points such as special-shaped packaging and aseptic filling, but also promotes the industry's transformation from "equipment supplier" to "packaging solution service provider" through data-driven operation and maintenance model. In high value-added fields such as biomedicine and high-end daily chemicals, Oushuo equipment has become the core guarantee for enterprises to pass international certifications such as FDA and EMA.